As far as Chinese injection molding is concerned, parting lines is a hot topic among product designers. In this article, we are going to discuss how you can determine the parting lines when working on an injection mold-designing project.
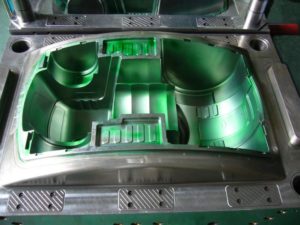
When working on a 3D CAD model, it’s not a good idea to avoid giving any consideration to the location of the parting line as it can have an impact on the project.
Complex Shapes
For complex shapes, it’s even harder to determine the location of the parting line. When designing a complicated part, parting line is important as molders and designers look at these parts in a different manner.
Molders will share your interest while producing the highest quality part. To achieve this purpose, it’s important to mold it properly. The designers will handle the designing part. Their job is to make sure it works well after the molding stage. The parting line location has an impact on both of the stages.
One role of the parting line is to determine the direction of the opening of the mold. Secondly, it has an impact on vestiges as well. Thirdly, it can have an impact on the cost of the molding and secondary operations.
LSR Parts
Designing parts for LSR molding is like the thermoplastic molding. However, for liquid silicone rubber, more preparation is required to prevent flash. LSR tends to flow into the relevant mold in the form of liquid. It will fill into the gaps as well. Although the parting lines on the components of LSR are not as visible, it is hard to prevent them. So, we suggest that you make sure that they are located on the sealing surface. This will help you produce cleaner parts in an efficient manner.
Know the Parting Lines
You can use many ways to address the challenges associated with the parting lines. First of all, you need to be aware of the important of the subject. As said earlier, the location of parting line is clear in most parts.
For complex parts, some tools in the CAD packages can help you locate the split lines. If you can’t do it yourself, you can hire an online service. To save money, you can give a go to a Chinese mold service as well.
Lastly, it’s important to keep in mind that the suggested parting line doesn’t have to be your sole option. The reason is that neither the design software nor the CAD programs know how the part will be used. So, it’s better to look at the parting lines with full attention, which will help you find out if it can work well as far as the functionality goes. If improvement are needed, you can us other design options. Alternatively, you can make changes to the design to create a better parting line based on your desired application.
Long story short, this was a brief explanation of how you can the parting lines when working designing different types of injection molds.
Chinese mold are quite popular in the here and now. If you are looking to save costs, you can check out some Chinese molds as well.
Resource box: This article is originally posted in http://www.chinainjectionmold.com.